SinterCast System 4000
The newly upgraded, fully automated System 4000 is comprised of individual hardware modules that can be configured to suit the layout, process flow and production volume of any foundry, both for ladle production and pouring furnaces. The System 4000 provides a flexible, robust and accurate hardware and software platform that enables the foundry to independently control CGI series production and product development.
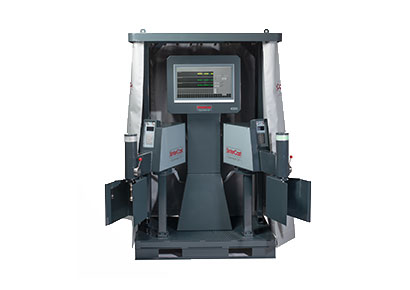
System 4000
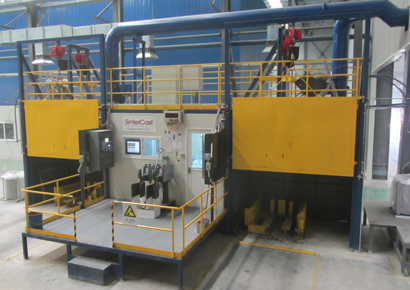
System 4000 Plus
System 4000 and System 4000 Plus
The basic configuration of the System 4000 consists of one Sampling Module (SAM), one Operator Control Module (OCM), a Power Supply, and a network-linked Wirefeeder for automated addition of magnesium and inoculant prior to casting. This configuration provides sampling capacity for approximately 15 ladles per hour.
Fully Flexible
The System 4000 can be configured with multiple Sampling Modules for increased throughput. Additional viewing options are available to display process information in different areas of the foundry. The System 4000 can be pallet-mounted, individually floor-mounted, or wall-mounted to suit any foundry layout.
System 4000 Plus
Based on the automatic input of base iron chemistry, ladle weight, iron temperature, and the historical SinterCast results, the newly upgraded System 4000 Plus calculates and adds the optimal amount of magnesium and inoculant cored wire in the initial base treatment. Automated base treatment prior to the measure-and-correct process control strategy enables foundries to reduce the variation of the base treatment process, thereby preventing operator error and improving the efficiency and productivity of the CGI series production process. The basic configuration of the System 4000 Plus consists of two Sampling Modules to obtain the thermal analysis samples, an Operator Control Module for data display and operator interaction, a Power Supply, two separate network-linked Wirefeeders for base treatment and correction, and a Peripheral Input Module for the collection of input data such as chemistry, ladle weight and iron temperature for base treatment and post-treatment data such as pouring temperature and time. This configuration provides sampling capacity for approximately 15 ladles per hour. Additional hardware can be added to accommodate each foundry layout and production throughput.
User-Friendly
System 4000 displays magnesium, inoculant and carbon equivalent results as histogram run-charts with all information in the local language. Highly visible Signal Lamps are used to communicate with the operator for ease of use operation.
Software Access – Independent Control
Foundry supervisors have full access to the process parameters, directly from their desktop computers, allowing the foundry to independently develop and calibrate new products and to modify parameters with series production. Measurement results from every ladle are available for direct transfer to the foundry quality control IT system in real-time to satisfy QS9000 traceability requirements.
Independent Maintenance
Supervisors and maintenance personnel can connect a configured laptop directly to the System 4000 to conduct full diagnostic testing and troubleshooting. The software used for the on-site testing is the same that SinterCast uses to certify modules and complete systems prior to delivery.
Documentation
Comprehensive manuals are available for the operators and supervisors describing the operation and maintenance of the System 4000. The Supervisor (Technical Reference) Manual provides detailed information on the use of the software, the access menus, and maintenance and troubleshooting. A Components Catalogue is provided to describe the hardware modules and individual components that can be sourced as spare parts.
Download PDF
- Data Sheet: SinterCast System 4000
- Data Sheet: SinterCast System 4000 Plus