SinterCast Tracking Technologies
With our roots in precision measurement in the demanding foundry environment, SinterCast® has expanded its technical offering to include a suite of traceability solutions that enable foundries to track ladles, moulds, castings and even the performance of individual operators. These technologies provide the ability to measure every step of the foundry process, and to use these measurements to determine and implement corrective actions that resolve the root cause of defects and process bottlenecks.
The SinterCast Tracking Technologies can be applied to grey iron, ductile iron and CGI foundries, and also to other metallurgical facilities such as steel mills.
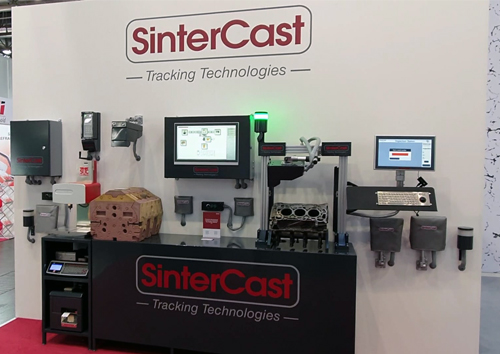
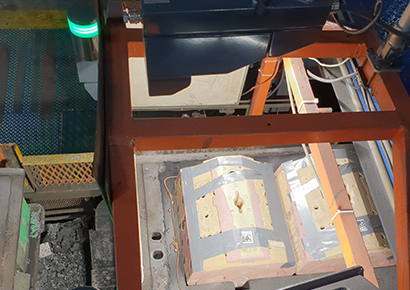
SinterCast Ladle Tracker®
RFID tags or optical 2D matrix plates are affixed to each ladle and RFID readers or optical cameras are located at key locations in the foundry to track the time and location of every ladle as it moves through the process. The technology automatically ensures that every ladle has successfully passed each step (temperature is correct, weight is correct, Mg-treatment was successful, time is within pre-set limits). If any step has not been successfully completed, the pouring car can be automatically blocked, without relying on behaviour of the operator. Ladle Tracker enables foundry managers to identify where (and why) any ladle falls out of the process, allowing corrective actions to be implemented to eliminate bottlenecks and to optimise process efficiency. All results are available for downloading, streaming to the foundry quality or ERP system, or viewing in real-time on any device that is connected to the internet, such as a mobile telephone.
SinterCast Cast Tracker®
Labelling of cores, combined with RFID or optical identification of each flask provides complete traceability of every casting. This traceability includes the date and time of core production (inception), shelf storage time, pouring (birth) and shake out. Together with the Ladle Tracker technology, Cast Tracker links the coremaking and moulding history to the liquid metal history, providing complete process traceability. For the foundry, Cast Tracker provides the detailed information (such as cast sequence) needed to determine robust correlations between casting defects and process parameters. For the OEM end-user, this novel capability provides complete traceability of every casting.