Business Model
CGI Business Model
SinterCast sells or leases the hardware, leases the process control software, sells the sampling consumables, and charges a running Production Fee for each tonne of CGI castings produced using the SinterCast technology. Revenue is also derived from spare parts, customer service, field trials and sales of test pieces. The individual components of the CGI business model are described as follows:
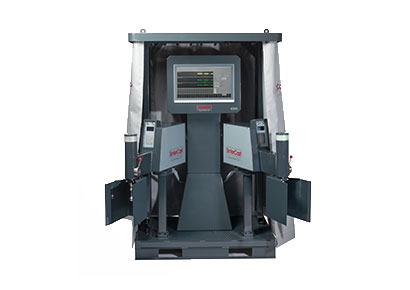
System 4000
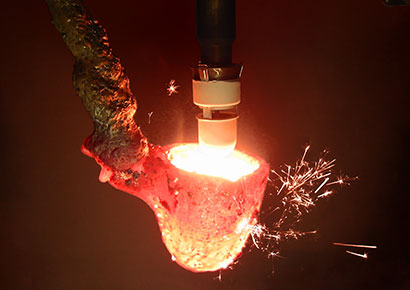
CGI Sampling
- System 4000 Hardware Platform: The System 4000 can be configured to suit the layout and process flow of any foundry. Typical sales prices are €400,000–600,000 for the full System 4000 or System 4000 Plus, and €75,000–125,000 for the Mini-System 4000, depending on the configuration and installation requirements. For leased systems, the typical lease period is seven years, but the duration can vary.
- Process Control Software: The software applies the metallurgical know-how and provides the operating logic for the System 4000 hardware. SinterCast charges an Annual Software License Fee and retains ownership of the software.
- Sampling Consumables: The consumables consist of the Sampling Cup and the Thermocouple Pair. One Sampling Cup is consumed with each measurement. The Thermocouple Pair is re-used for up to 250 measurements. One SinterCast measurement is required for each production ladle.
- Production Fee: A running fee is levied for each tonne of shipped castings, based on the as-cast (pre-machined) weight. There are 20 Engine Equivalents (50 kg each) per tonne.
- Technical Support: SinterCast provides engineering service for product development, trials, new installations, calibrations, metallurgical consultancy, and ongoing customer service.
The total running fees (sampling consumables, software licence and Production Fee) depend on the ladle size and the casting yield. The SinterCast business model is highly scalable, allowing profitability to rise as the installed base grows and as more products enter series production.
Tracking Technologies Business Model
Introduced in 2016, the Tracking Technologies include the SinterCast Ladle Tracker® and the SinterCast Cast Tracker®. As of the end of 2021, four Ladle Tracker and two Cast Tracker systems have been installed in six foundries in five countries. The SinterCast Tracking Technologies offer the potential to provide supplemental income to the core CGI business and to enhance the technical reputation of SinterCast as a provider of innovative solutions to improve process control and profitability in the foundry industry.
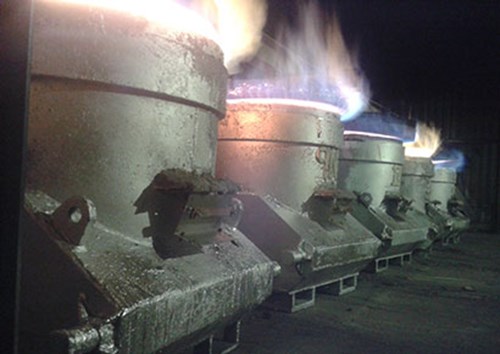
SinterCast Ladle Tracker®
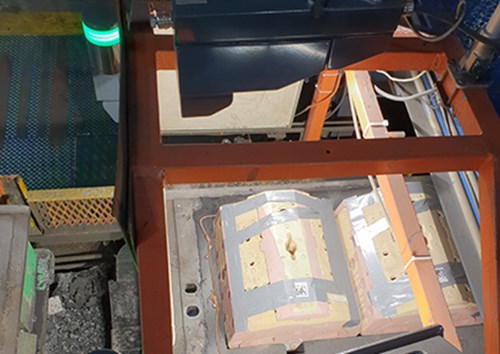
SinterCast Cast Tracker®
- Ladle Tracker: The SinterCast Ladle Tracker measures the time and location of every ladle as it moves through the foundry. Radio Frequency Identification (RFID) tags are affixed to each ladle and antennae are positioned at key locations in the foundry to ensure that every ladle successfully passes every step. The Ladle Tracker technology prevents out-of-spec iron from being poured and enables foundry managers to identify bottlenecks and to implement process efficiency improvements.
- Cast Tracker: The SinterCast Cast Tracker provides complete traceability of the foundry process, linking the coremaking and moulding history to the liquid metal history. The traceability includes the date and time of core production (inception), shelf storage time, pouring (birth) and shake out. The Cast Tracker technology prevents out-of-spec moulds from being poured, and provides a comprehensive database for traceability, troubleshooting and process optimisation.
- Revenue Stream: As in the CGI business model, SinterCast sells or leases the Tracking Technologies hardware. Depending on the configuration and scope of the installation, the sales price may range from approximately €75,000–200,000. SinterCast charges an Annual Software Licence Fee and retains ownership of the process control software. SinterCast also provides RFID tags and labels as consumables, but the consumable volume and revenue are limited. A running fee for each casting has been established for the Cast Tracker technology, but a running fee is not applicable for the Ladle Tracker technology.